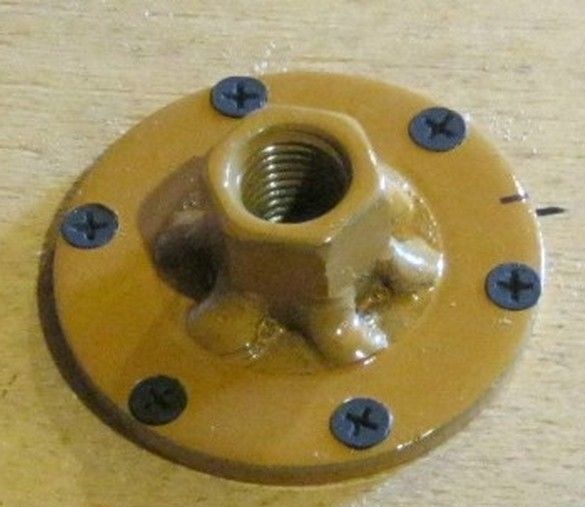
Etter å ha konstruert tre dreiebenk, hadde det gøy med enkel sving i sentrene. Etter en stund ble det nødvendig å behandle mer forskjellige arbeidsstykker. Jeg måtte flytte hjernen min, som om jeg fra improviserte midler, uten tilgang til en tredjepart dreiebenk (for metall), skulle lage det riktige utstyret. En av designene viste seg å være veldig billig, praktisk og etterspurt.
Snap-in-armaturen var ofte sammensatt av to deler - en universal liten metallplate og en spesialisert tredel. En metallplate kan også brukes, som vanlig, ved å feste skruer på arbeidsstykket.
Hva ble brukt.
Verktøy.
Selve trebenken, kuttere for den, et sett med benkverktøy. Du kan ikke klare deg uten en skjæremaskin (kvern), det er bedre å bruke en liten - den er mer praktisk og tryggere. Hodetelefoner for både skyting og beskyttelsesbriller eller visir. Ikke komme deg ut uten henholdsvis sveising - en liten omformer og tilbehør. Elektroder 2,5 mm. Ofte brukt varmesmelt. Det er nødvendig at verken skal være boring, mer praktisk og mer nøyaktig, det er klart, maskinen.
Materialer.
Egentlig bare riktig antall muttere og skiver. Det er bedre å male det ferdige metallstykket, så pluss maling. Et lite tre for "smal spesialisering", jeg bruker ofte tørt bjørkeved med jevne lag.
So. Spindelen på dreiebenken min ender med en M16-tråd, som tillater bruk av standard maskinvare. I dette tilfellet er dette en "utvidelsesmutter." Den kuttes i to på direkte på maskinen, slås på og roterer. Vinkelsliper. Den skal kuttes forsiktig. Først på en slått av maskinen og med en tomgangskvern i hendene, prøv forsiktig på, slik at det er praktisk, albuene uansett hvor du står og for ikke å passe inn i noe som roterer.
Maskinen slås på og etter å ha tatt i bruk en ferdig testet positur, slått på med en kvern, slår vi et merke på markøren midt i den roterende mutteren. Spesielt forsiktig med det første, til kantene er saget, så begynner det å skjære jevnere og trykket kan økes litt.
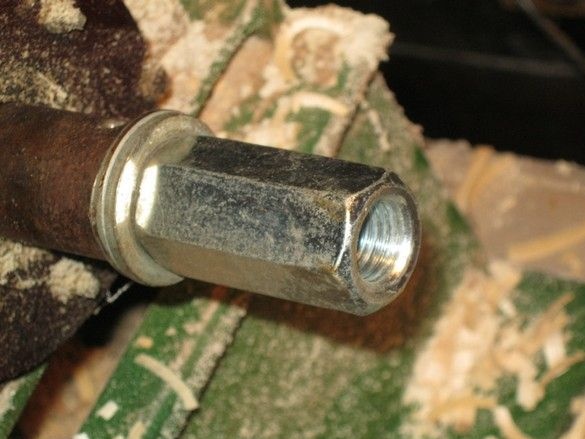
Etter litt tid på innsatsen blir veggen til mutteren skåret gjennom og halvparten faller bort.Høyden på hver halvdel, tatt i betraktning kuttets bredde, viser seg å være litt større enn den vanlige søsteren som ikke er “forlengelse”. Lengden på tråden på spindelen til maskinen min tillater ikke bruk av en vanlig mutter - den stikker ut under den ferdige frontplaten og forårsaker mye ulempe senere, når du jobber.
Neste trinn blir sveising. Fra standardutvalget av maskinvare tar jeg en "forsterket skive", i noen butikker kalles det en "kroppsskive" med passende diameter. Vanligvis er dette nesten det største av det tilgjengelige sortimentet. Du må sjekke om mutteren faller i den. Mutteren skal stå i midten av hullet i skiven. En kuttet mutter vil stå bedre - det vil ikke være noen avfasning på den ene siden av den, dette bør tas i betraktning når du prøver på en ny i butikken.
Den avskårne halvparten er sveiset til skiven. Pent. Det er veldig bra å først stramme dem med en klemme, men vanligvis viser det seg ganske bra. Ribbene er sveiset i følgende rekkefølge - hvilken som helst, så motsatt. Arbeidsstykket roterer 90 grader, igjen en av de to, så motsatt. Så det er mindre sjanse for at mutteren glir av skiven. Egentlig prøvde jeg i de første eksemplarene å organisere "noten" med den samme kvernen på den roterende halvdelen av mutteren, for en sikker passform i hullet, men vinkelsliperen er ikke verktøyet som kan gjøre denne jobben godt - ofte på grunn av den ikke så jevn kant på "rillen" , var mutteren ikke veldig på linje med skiven.
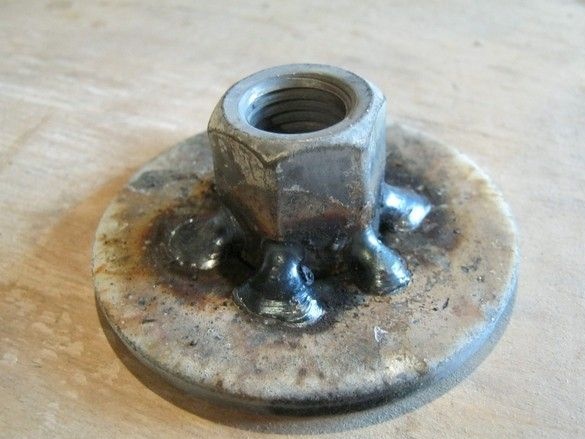
Etter å ha avkjølt arbeidsstykket, omslutter vi som vanlig glassskorpen med slagg og legger arbeidsstykket på maskinens spindel, under rotasjon vurderer vi utkjøringen, hvis de er innenfor rimelige grenser, korrigerer vi den medfølgende vinkelsliperen.

Det er mulig for estetikk og på motsatt side. Her, skjerping med en blyant på rett sted for det roterende arbeidsstykket, noterer vi oss diameteren som hullene vil bli boret på. For å bruke den fremtidige frontplaten med relativt store gjenstander, kan de bores mer, opptil seks, hvis det gjelder bagateller - tre, fire.
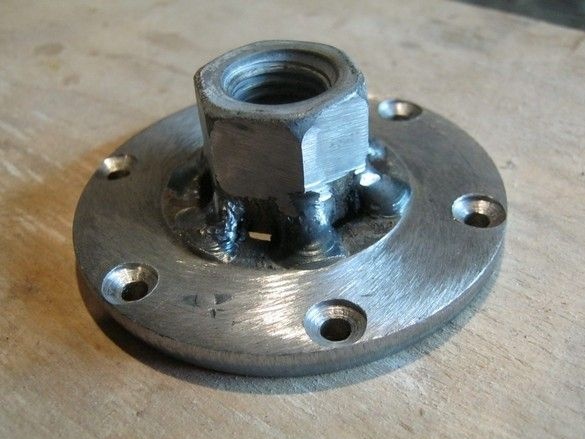
Etter det ville det vært fint å male til det er rust - sinklaget er delvis brent, delvis drenert. Under spratt "oker" fra en sprayboks, i to lag, selv om jeg vanligvis er lat.
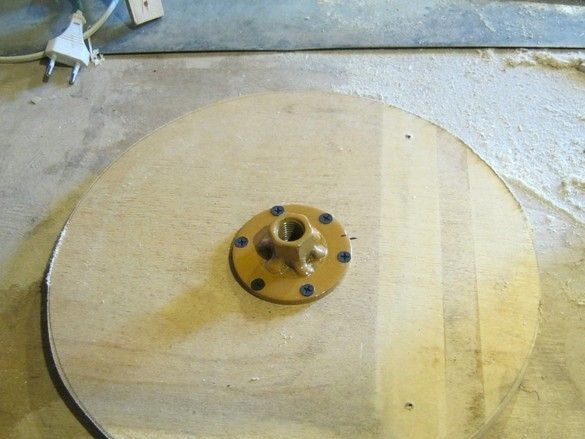
På bildet er den ferdige frontplaten på slipeskiven laget av tykk kryssfiner. På en disk undertrykkelse limes PVA-lim, mellomstor, et sandpapir på fillebasis. Gjennom et lag aviser slik at du kan rive av den slikkede svetten.
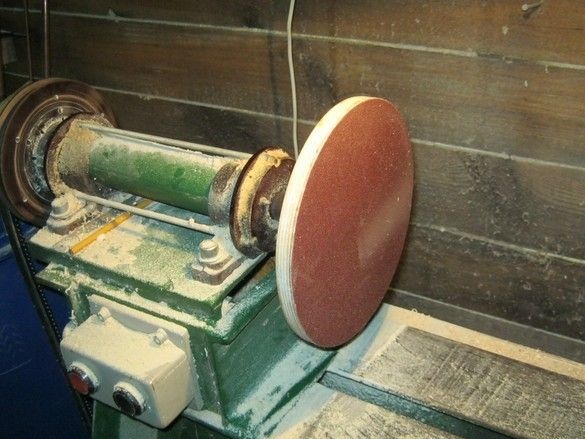
For å slipe verktøyet, må du montere små trebiter før liming.
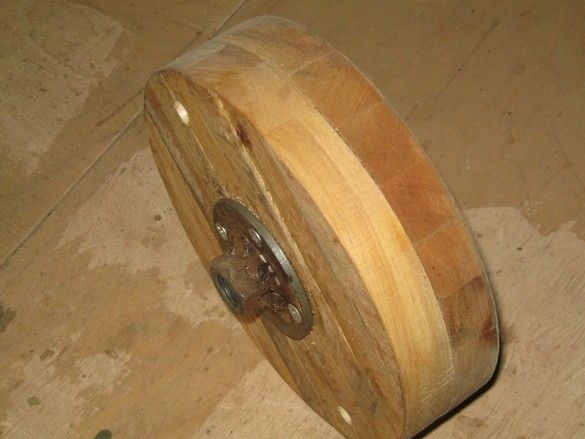
En lignende kontrast, men mindre i diameter og limt fra bjørkeblokker i to lag med overlapping. For skjerping av dreieverktøy. På slutten er det samme sandpapir, et lærbelte limes langs omkretsen for finjustering med GOI-pasta.
Og til slutt bruken av frontplaten vår for det nåværende arbeidet. Som den vanlige, er vår lille praktisk å bruke der du trenger å montere arbeidsstykket i den ene kanten, uten bakre senter. Samtidig er det veldig praktisk å lime arbeidsstykket til mellomblokken. Et stykke av brettet er ikke festet med lange skruer og dreies til en praktisk diameter, arbeidsstykket er allerede limt på det. Smeltlim.
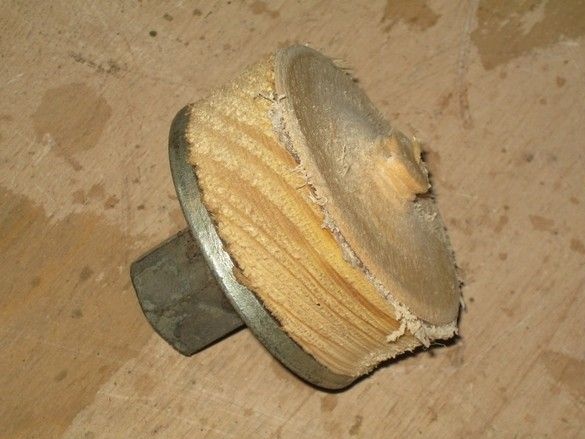
På bildet er det en slik "kassett", med en avling som er igjen fra arbeidsstykket. Før du limer den neste, settes frontplaten inn i maskinen og "kuttes av" med et skjæreverktøy, og kutt restene av den limte. Samtidig er det nødvendig å fange en del av det gamle klebende laget slik at det (limet) ikke samler seg for mye.
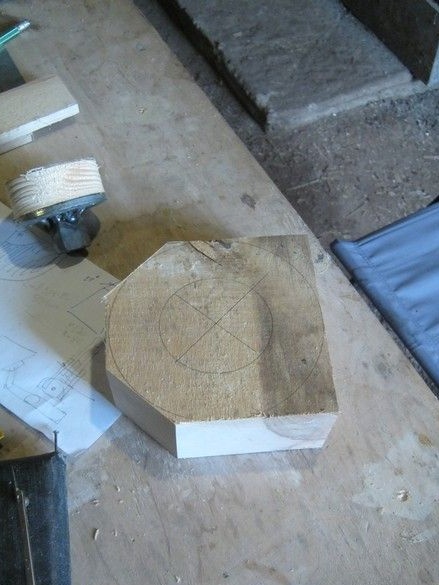
Arbeidsstykket er merket, mens blant annet et kompass, en sirkel med diameter tegnes litt større enn "blokken" på frontplaten. Dette lar deg orientere den nøyaktig når den er limt.
Jeg smører begge overflater som skal limes med varmt lim, ikke nødvendigvis helt, omkretsen rundt omkretsen er nok, centimeterne rygger bort fra kanten.
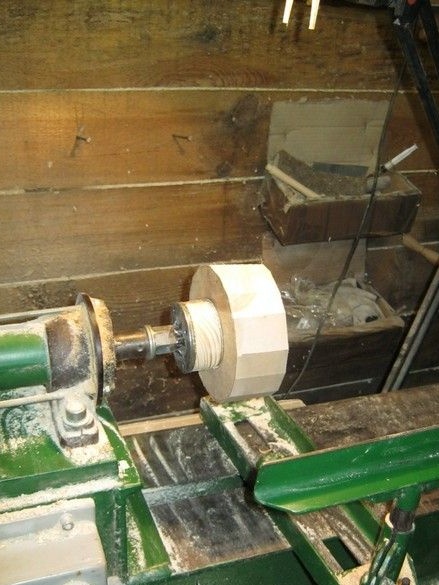
Til å begynne med, før fullstendig "lure", er det bedre å trykke arbeidsstykkets baksenter, og deretter, når det ikke er støtbelastning, fjernes det.
Det fine med en slik installasjon er gjennom blokken, i de betydelig mer økonomiske utgiftene til arbeidsstykkematerialet, dessuten, når du svinger, trenger du ikke hele tiden å huske hvor lenge skruene er for ikke å klatre kutteren til deres dybde.
Vel, til dessert - det er flere alternativer for et mer spesialisert verktøy basert på den produserte frontplaten.
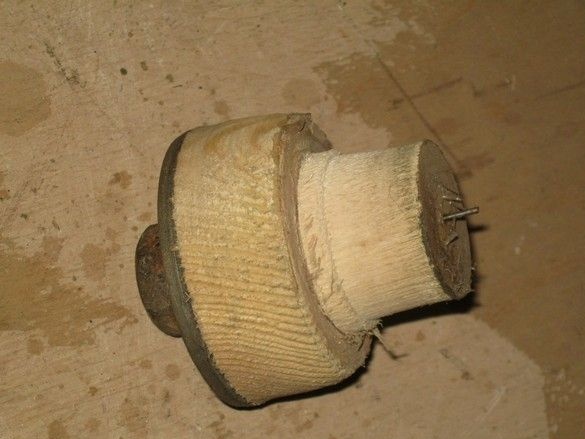
For eksempel, denne, ble det påkrevd at noe snudde veldig presist rundt det eksisterende senteret - like enkelt som avskalling av pærer.
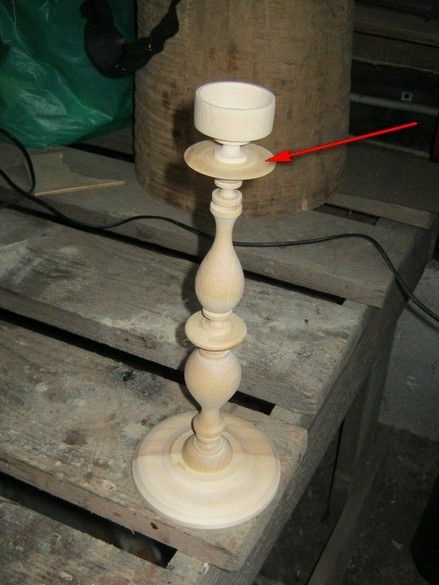
Eller for eksempel - en del av en lysestake laget av 6mm kryssfiner eller en tynn bjørkeplate. For en klemme og prosessering ble en slik snap gjort.
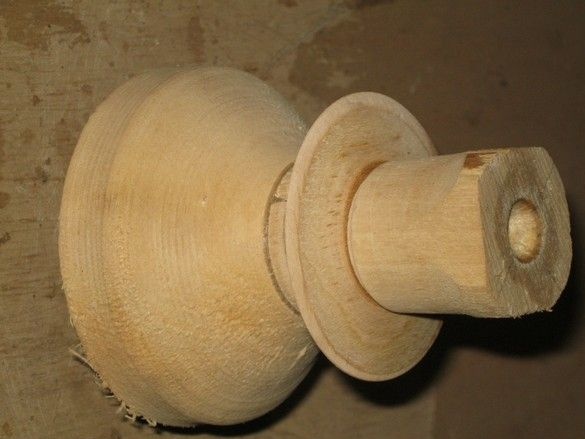
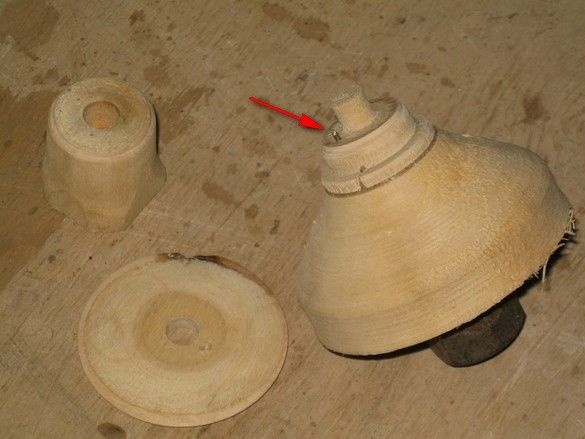
Skarpe fedd hindrer arbeidsstykket i å vri seg. Sett sammen, strammet av baksiden.
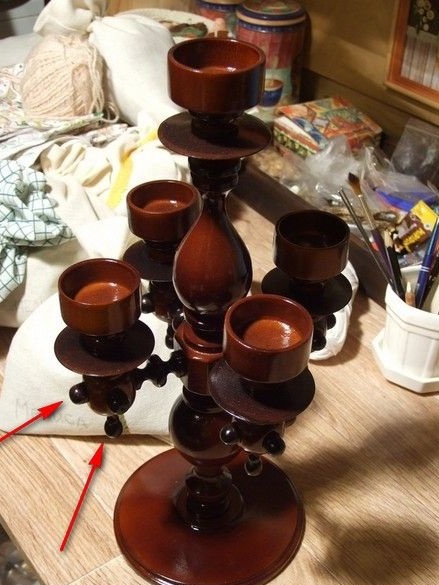
Ved fremstilling av lysekronen var det nødvendig med en rekke små deler, for eksempel navler, jeg måtte lage en enkel tre chuck-hylse.
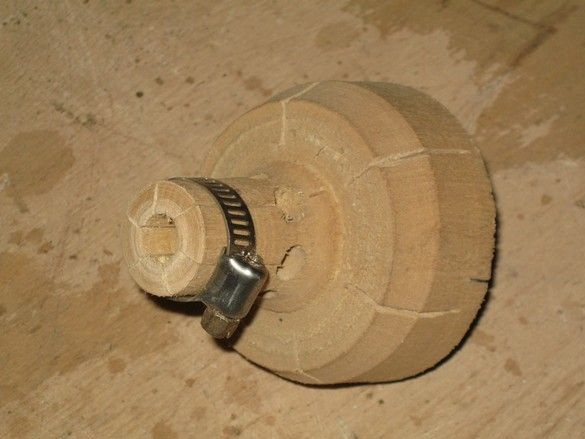
Til tross for de noe begrensede egenskapene, har den også en rekke fordeler, nemlig fremstillingsvennlighet og lave kostnader. Når du behandler miniatyrdeler, i nærheten av mest "kjever", skal man ikke være for redd for å hekte “kassetten” med et verktøy, som i tilfelle av bruk av en metallfabrikkanalog noen ganger har fatale konsekvenser. Ja, sikkerhet er igjen et minimum av utstående deler, de kan reduseres enda mer hvis du bytter ut en metallormklemme med glødet stål eller kobbertråd eller til og med lager en smal avsmalning på utsiden av kjevene og fyller ringen for klemme. Metall eller tre.
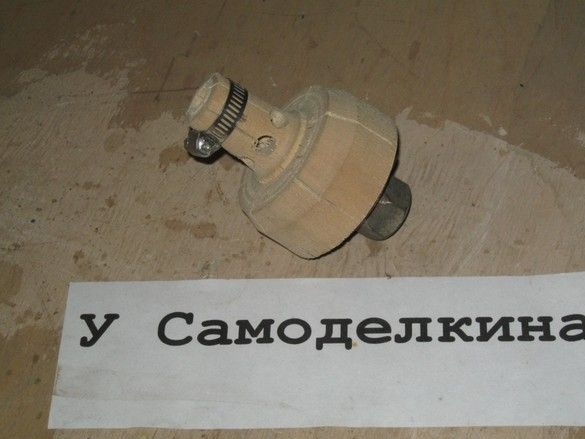
Ved fremstilling av en hylse chuck blir sylinderen først dreid, et sentralt hull (en boremaskin) blir boret, hull merket og boret på siden. Deretter, i dreiebenken, blir den fremtidige klemmen maskinert - ikke-tykke kjever dannes. Til slutt gjorde han kutt av kollbladene.